WHY SMART INVESTMENTS IN TECHNOLOGY AND MAINTENANCE OUTWARD THE SEMA SPECTACLE
ARTICLE BY STEFANO LIESSI
When you are concerned about your return on investment (ROI), one of the best ways to invest is to buy the latest and greatest “Unicorn Fix-All 2000”. It is the answer to all your problems.
Of course, you want to make sure you research the item, use a reputable source to review your purchase, and if you are buying from SEMA, make sure it is compliant with Canadian Standards Association (CSA) requirements. In this case, also make sure your supplier is able to service and maintain the equipment. Too often, people buy equipment and then stop caring about it or maintaining it. Year after year, I see the same scenario play out. As I walk in and out of stores, I see it never stopping.
Me: “What do you think of [INSERT GEAR HERE]?”
Technician: “I don’t know, I haven’t used it.”
Me: “Why?”
Technician: “I don’t know. Broken.” I’ve noticed this before, due to the dust on it and the fact that it’s behind other objects that have been neglected for a long time. Let me be clear: this scenario is much more common than you might think. Over the years, I’ve been confronted many times with a poorly maintained welding station. Yes, of course, the welder is necessary for the course. Can you imagine my surprise? Well, no. I’ve become somewhat desensitized to these types of scenarios.
This is where the training sessions start to pay off. I hear the same things over and over again: “I’ve been doing this for years. Why am I wasting my time?” “My guy is the best; he’ll do it without a problem.” “We need this for OE certification.” “Do you think we can get this done by noon?”
Occasionally I meet a technician with this mindset. However, while owners and managers often exhibit this thought process, technicians are usually interested in learning new skills to improve themselves; it’s hard to make a living. Imagine a busy week, no more class to wait for. So here we are with a group of technicians, a class scheduled, and a welder that’s down. What happens then?
As an instructor, I ask how many employees are familiar with the welding application we are testing that day. The general response is, “I’ve done it a few times, I used it in my other shop.” My response: “Great, then you’ll know how we can get around this situation.”
The condition of the equipment has already led me to conclude that there is little to no experience; the welder is inoperable and there is no backup welder. This is the hidden agenda of RSI training and knowledge; certification sessions are not just a plaque on the wall. A good, qualified technician knows when something is wrong and knows how to correct the problem or find a workaround to get by temporarily–not for two years.
Every time I run a session, part of the day is spent discussing processes, OE procedures, equipment usage, and maintenance. Knowing that this is part of the certification, the ENP assumes and expects it. In this specific example, all was not lost; I was able to set things up and explain to the technicians how to temporarily work around this issue, and hopefully the knowledge was retained.
It takes a genuine interest in a subject to retain the relevant information and achieve consistent success; it takes time and effort. It’s much more than a 15 minute YouTube video. To be perfectly fair, if you have technicians who don’t understand and know the processes and how to use the equipment, and your equipment is inoperable or barely operable, then you’re not repairing vehicles properly or to OE standards… you’re not OE certified.
As instructors or trainers, we cannot be responsible for what you do with your knowledge after the fact. All we can do is try to make you understand the relevance of the information and how it relates to your daily business. Take the car owner: he has no idea, but we, as an industry, do. The customer relies on the cutting-edge equipment you advertise. He trusts you and that is what he is there for.
What does this have to do with ROI? Quite simply, I tell you to invest in the right things and get a faster ROI. The right things are your technicians and the maintenance of your equipment.
If the technician comes to tell you how much you need for a piece of equipment that, if used properly, will improve the process, don’t respond by saying, “Do we really need that?” Instead, ask for an explanation and try to come to a mutual understanding. In my opinion, and you are entitled to my opinion, the smaller investment in your technicians and maintenance will extend the life of the Unicorn Fix-All 2000 and pay dividends. You rely on your technicians to run the machine; your technicians rely on the equipment to run things; there is absolutely no point in buying a new Unicorn Fix-All 2000 if you don’t keep your equipment and technicians well maintained. Take that investment and clean up your yard; I bet you’ll get a much better return on your investment.
In this scenario, I imparted valuable information to these young people, teaching them how to keep equipment up to date and making them realize that understanding the importance of maintaining shop equipment is part of the value of good training. It will require some investment on the part of the shop, but it is well worth it. When you purchase another “Unicorn Fix-All 2000,” it is supplementing your maintained equipment rather than replacing it.
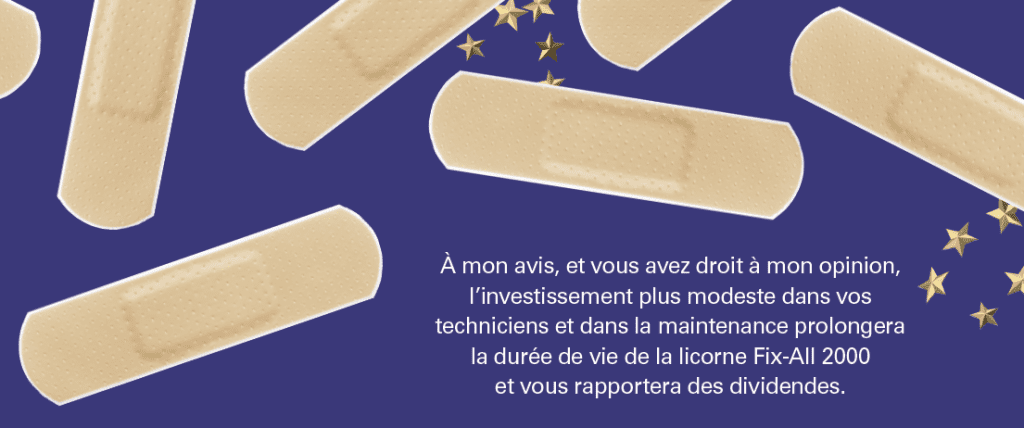
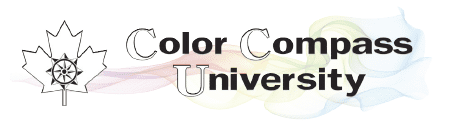
